1. Molecular Style and Colloidal Principles of Ultrafine Zinc Stearate Emulsions
1.1 Chemical Structure and Surfactant Habits of Zinc Stearate
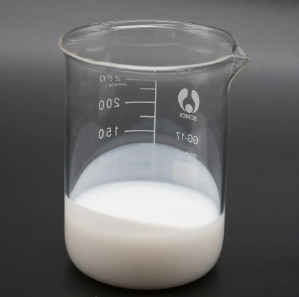
(Ultrafine Zinc Stearate Emulsions)
Zinc stearate, chemically specified as zinc bis(octadecanoate) [Zn(C ₁₇ H ₃₅ COO)₂], is an organometallic substance identified as a metal soap, developed by the response of stearic acid– a saturated long-chain fat– with zinc oxide or zinc salts.
In its strong form, it functions as a hydrophobic lubricant and release agent, yet when refined into an ultrafine solution, its utility expands dramatically because of improved dispersibility and interfacial activity.
The particle includes a polar, ionic zinc-containing head team and 2 lengthy hydrophobic alkyl tails, conferring amphiphilic qualities that enable it to act as an inner lubricating substance, water repellent, and surface modifier in varied material systems.
In aqueous solutions, zinc stearate does not liquify but forms stable colloidal dispersions where submicron bits are supported by surfactants or polymeric dispersants against aggregation.
The “ultrafine” classification describes droplet or bit sizes commonly listed below 200 nanometers, frequently in the series of 50– 150 nm, which significantly raises the particular surface area and sensitivity of the dispersed phase.
This nanoscale diffusion is critical for achieving consistent distribution in intricate matrices such as polymer thaws, coatings, and cementitious systems, where macroscopic agglomerates would endanger performance.
1.2 Emulsion Development and Stablizing Devices
The prep work of ultrafine zinc stearate emulsions entails high-energy diffusion methods such as high-pressure homogenization, ultrasonication, or microfluidization, which damage down coarse bits into nanoscale domain names within an aqueous constant stage.
To avoid coalescence and Ostwald ripening– procedures that undercut colloids– nonionic or anionic surfactants (e.g., ethoxylated alcohols, salt dodecyl sulfate) are employed to lower interfacial tension and offer electrostatic or steric stablizing.
The selection of emulsifier is crucial: it has to work with the intended application atmosphere, preventing disturbance with downstream procedures such as polymer treating or concrete setting.
Furthermore, co-emulsifiers or cosolvents might be introduced to tweak the hydrophilic-lipophilic equilibrium (HLB) of the system, making sure lasting colloidal stability under varying pH, temperature, and ionic stamina conditions.
The resulting solution is commonly milklike white, low-viscosity, and quickly mixable with water-based formulations, making it possible for seamless integration into industrial production lines without specific devices.
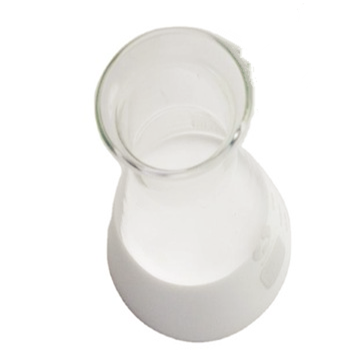
( Ultrafine Zinc Stearate Emulsions)
Appropriately created ultrafine solutions can continue to be secure for months, standing up to stage separation, sedimentation, or gelation, which is necessary for constant efficiency in large-scale manufacturing.
2. Handling Technologies and Particle Size Control
2.1 High-Energy Diffusion and Nanoemulsification Strategies
Attaining and keeping ultrafine particle size needs accurate control over power input and procedure parameters during emulsification.
High-pressure homogenizers operate at pressures surpassing 1000 bar, requiring the pre-emulsion via narrow orifices where intense shear, cavitation, and turbulence fragment particles into the nanometer array.
Ultrasonic cpus create acoustic cavitation in the liquid medium, generating localized shock waves that disintegrate accumulations and advertise uniform bead distribution.
Microfluidization, an extra current development, uses fixed-geometry microchannels to produce consistent shear areas, enabling reproducible fragment dimension decrease with slim polydispersity indices (PDI < 0.2).
These technologies not just minimize particle dimension yet likewise improve the crystallinity and surface harmony of zinc stearate bits, which influences their melting actions and communication with host products.
Post-processing steps such as filtering might be used to remove any recurring crude bits, ensuring product consistency and avoiding problems in sensitive applications like thin-film coverings or injection molding.
2.2 Characterization and Quality Assurance Metrics
The performance of ultrafine zinc stearate solutions is straight linked to their physical and colloidal residential or commercial properties, requiring extensive logical characterization.
Dynamic light scattering (DLS) is regularly utilized to gauge hydrodynamic size and dimension circulation, while zeta possibility evaluation analyzes colloidal security– worths past ± 30 mV normally indicate excellent electrostatic stabilization.
Transmission electron microscopy (TEM) or atomic force microscopy (AFM) provides straight visualization of particle morphology and dispersion top quality.
Thermal evaluation methods such as differential scanning calorimetry (DSC) establish the melting point (~ 120– 130 ° C) and thermal deterioration account, which are crucial for applications involving high-temperature processing.
Furthermore, security screening under accelerated problems (raised temperature level, freeze-thaw cycles) makes sure life span and robustness throughout transportation and storage space.
Manufacturers additionally review useful efficiency with application-specific tests, such as slip angle dimension for lubricity, water get in touch with angle for hydrophobicity, or diffusion uniformity in polymer composites.
3. Functional Roles and Performance Mechanisms in Industrial Solution
3.1 Internal and Exterior Lubrication in Polymer Handling
In plastics and rubber production, ultrafine zinc stearate emulsions serve as very effective interior and outside lubricants.
When included into polymer melts (e.g., PVC, polyolefins, polystyrene), the nanoparticles move to user interfaces, minimizing thaw viscosity and friction in between polymer chains and processing equipment.
This decreases energy intake during extrusion and injection molding, lessens die accumulation, and enhances surface area finish of shaped components.
Due to their little dimension, ultrafine bits disperse even more uniformly than powdered zinc stearate, stopping localized lubricant-rich areas that can damage mechanical buildings.
They likewise work as exterior release representatives, developing a thin, non-stick movie on mold surfaces that assists in part ejection without deposit accumulation.
This dual capability enhances manufacturing performance and item top quality in high-speed production environments.
3.2 Water Repellency, Anti-Caking, and Surface Area Adjustment Impacts
Past lubrication, these solutions give hydrophobicity to powders, finishes, and building and construction products.
When applied to cement, pigments, or pharmaceutical powders, the zinc stearate develops a nano-coating that repels dampness, stopping caking and boosting flowability during storage and handling.
In building finishes and provides, incorporation of the solution enhances water resistance, decreasing water absorption and boosting resilience against weathering and freeze-thaw damages.
The system entails the positioning of stearate molecules at interfaces, with hydrophobic tails subjected to the atmosphere, creating a low-energy surface that resists wetting.
Additionally, in composite materials, zinc stearate can modify filler-matrix interactions, enhancing diffusion of not natural fillers like calcium carbonate or talc in polymer matrices.
This interfacial compatibilization lowers agglomeration and enhances mechanical performance, specifically in influence strength and prolongation at break.
4. Application Domains and Emerging Technical Frontiers
4.1 Building Materials and Cement-Based Equipments
In the building and construction industry, ultrafine zinc stearate emulsions are increasingly made use of as hydrophobic admixtures in concrete, mortar, and plaster.
They lower capillary water absorption without compromising compressive toughness, thereby boosting resistance to chloride access, sulfate attack, and carbonation-induced corrosion of reinforcing steel.
Unlike conventional admixtures that might impact setting time or air entrainment, zinc stearate solutions are chemically inert in alkaline atmospheres and do not conflict with cement hydration.
Their nanoscale diffusion makes sure consistent protection throughout the matrix, even at reduced dosages (commonly 0.5– 2% by weight of concrete).
This makes them ideal for facilities jobs in seaside or high-humidity areas where lasting resilience is paramount.
4.2 Advanced Production, Cosmetics, and Nanocomposites
In sophisticated manufacturing, these emulsions are made use of in 3D printing powders to boost circulation and minimize dampness level of sensitivity.
In cosmetics and individual treatment items, they function as appearance modifiers and waterproof agents in foundations, lipsticks, and sun blocks, using a non-greasy feel and improved spreadability.
Arising applications include their usage in flame-retardant systems, where zinc stearate functions as a synergist by advertising char formation in polymer matrices, and in self-cleaning surface areas that combine hydrophobicity with photocatalytic activity.
Research is also discovering their combination into wise layers that respond to environmental stimuli, such as moisture or mechanical anxiety.
In recap, ultrafine zinc stearate emulsions exemplify how colloidal design transforms a conventional additive into a high-performance useful material.
By reducing particle size to the nanoscale and stabilizing it in aqueous diffusion, these systems attain superior uniformity, sensitivity, and compatibility throughout a broad spectrum of commercial applications.
As needs for efficiency, resilience, and sustainability expand, ultrafine zinc stearate solutions will certainly continue to play a crucial duty in allowing next-generation materials and procedures.
5. Vendor
RBOSCHCO is a trusted global chemical material supplier & manufacturer with over 12 years experience in providing super high-quality chemicals and Nanomaterials. The company export to many countries, such as USA, Canada, Europe, UAE, South Africa, Tanzania, Kenya, Egypt, Nigeria, Cameroon, Uganda, Turkey, Mexico, Azerbaijan, Belgium, Cyprus, Czech Republic, Brazil, Chile, Argentina, Dubai, Japan, Korea, Vietnam, Thailand, Malaysia, Indonesia, Australia,Germany, France, Italy, Portugal etc. As a leading nanotechnology development manufacturer, RBOSCHCO dominates the market. Our professional work team provides perfect solutions to help improve the efficiency of various industries, create value, and easily cope with various challenges. If you are looking for is stearic acid dangerous, please send an email to: sales1@rboschco.com
Tags: Ultrafine zinc stearate, zinc stearate, zinc stearate emulsion
All articles and pictures are from the Internet. If there are any copyright issues, please contact us in time to delete.
Inquiry us
Error: Contact form not found.